Composite Sheets For Pharmaceutical Manufacturer in China
Whether you are a pharmaceutical company, packaging company, or drug distributor, we are your trusted partner. Through our high-quality composite sheets, you can ensure the safety and effectiveness of drug packaging and provide a better user experience for end consumers.
Different Types Of Pharmaceutical Composite Sheets
Excellent PVC/PVDC Composite Sheet Brings Drug Stability
Excellent puncture and tear resistance effectively protects medicines from tampering and contamination. Compatible with most pharmaceuticals, these composite sheets are ideal for packaging and are also UV-resistant, preventing UV rays from affecting the efficacy and safety of medicines. At the same time, the use of such materials reduces packaging costs, with the savings invested in drug development.
Whether it is blister packs, bottles or flexible packaging, PVC/PVDC materials can provide flexible solutions to meet the packaging requirements of different drugs.
Material composition and characteristics:
● PVC: Provides strength, flexibility and clarity.
● PVDC: Enhances additional protection against moisture, oxygen and external contaminants.
Cold Forming Aluminum Foil
With excellent barrier properties, made of OPA/ALU/PVC laminated, it is a high barrier effect packaging material for high-end drugs/tablets/capsules.
Material Composition and Characteristics:
OPA: the outer layer provides good mechanical strength and abrasion resistance.
ALU: As the core layer, it effectively prevents oxygen, moisture and light from affecting the inside of the package.
PVC: As the inner layer, it is in direct contact with the medicine and maintains the stability of the medicine.
Common Structures for Cold Formed Aluminum Foil
OPA | 25μm | 25μm | 25μm |
AL | 47μm | 60μm | 47μm |
PVC | 60μm | 60μm | 60μm |
Cold Forming Aluminum Foil Production Process
The production of cold forming aluminum foils involves several key steps, from the selection of raw materials to the final manufacture of the foil. The following is an overview of a typical manufacturing process:
Raw material selection
The process starts with the selection of high-quality raw materials, including aluminum foil, polyamide (OPA) and polyvinyl chloride (PVC). These materials are selected based on their specific properties to meet the desired characteristics of the cold-formed aluminum foil.
Preparation of aluminum foil
Aluminum foil is usually purchased in large rolls. The rolls are unrolled and the foil is inspected for any defects or impurities. The aluminum foil may undergo a cleaning process to remove contaminants that may affect the final product.
Coating application
Aluminum foil is coated with a layer of polyamide (OPA) and polyvinyl chloride (PVC). The coatings are applied to both sides of the foil to ensure even coverage. The combination of these materials enhances the barrier, flexibility and overall performance of the foil.
Lamination process
Coated aluminum foils undergo a lamination process that firmly bonds the polyamide and PVC layers to the aluminum surface. Lamination is usually achieved by heating and pressurization, resulting in a strong, complete composite material.
Cold forming process
The composite material is then subjected to a cold forming process. Cold forming involves molding a material at a temperature below its recrystallization point. This process gives the foil rigidity so that it retains its shape and structure without becoming too pliable.
Printing (optional)
If desired, cold formed foils can undergo a printing process to imprint branding, product information, or regulatory markings. Printing is usually done with special inks that adhere well to the surface of the foil.
Cutting and slitting
Cold formed aluminum foils are cut or slit to the required size. This may vary depending on the specific application and packaging requirements. Cutting accuracy is critical to ensure consistency in the final product.
Quality Control
Throughout the manufacturing process, we implement quality control measures to ensure that cold formed aluminum foils meet specified standards. Checks may include thickness, coating uniformity, adhesion strength and overall structural integrity.
Packaging and Distribution
If desired, cold formed foils can undergo a printing process to imprint branding, product information, or regulatory markings. Printing is usually done with special inks that adhere well to the surface of the foil.
4 Factors in Selecting Cold Forming Aluminum Foil
✔ Superior Barrier Protection – Effectively blocks moisture, gases, and UV light to ensure product stability.
✔ Strong Sealing Performance – Compatible with various heat-sealing coatings for reliable adhesion to blister bases.
✔ Customizable Printing – Available in printed or unprinted options for brand differentiation and regulatory compliance.
✔ High Puncture Resistance – Ensures durability and prevents accidental ruptures.
Cold Forming Aluminum Foil Application
Item | Tablet | Capsule | Small Dose | Nutritional Supplement | Vaccines and Biopharmaceuticals | Children's Medicines | Antibiotic medicines | Hormone medicines |
Specific part | Blister Packaging | Aluminum Foil Blister Packs | Single-dose packaging | Tablet or capsule packaging | Vaccine Packaging | Small dosage packs (liquid or tablets) | Antibiotic medicines packaging | Hormone medicines packaging |
Details | Blister section: the tablets are placed in a blister and the aluminum foil layer is encapsulated to form a complete drug plate. | Blister section: Capsules are placed into each individual blister hole and aluminum foil seals the blister. | Individual blisters or sachets: each dose is packaged individually. | Blister section: tablets or capsules are individually encapsulated in a blister. | Vial cap closure or pouch sealing section: ensures that the vaccine is hermetically sealed. | Single-dose blister section: provides hermetic protection for single-dose packages of children's medicines. | Blister section: antibiotic tablets are individually encapsulated in a blister to maintain the quality of the drug. | Blister section: Hormone medicines are individually encapsulated in blisters to ensure the potency and stability of the medicines. |
Different Types of Composite Sheets For Pharmaceutical
Protecting The Efficacy and Quality Of Pharmaceuticals
As a pharmaceutical packaging material, cold-formed aluminum foil possesses excellent barrier properties, effectively preventing moisture, oxygen and ultraviolet rays from affecting pharmaceuticals. Through its powerful barrier effect, it is able to maintain the stability and active ingredients of medicines and prevent the quality of medicines from deteriorating or failing due to the external environment.
Whether it is tablets and capsules that are susceptible to moisture or light-sensitive medicines, cold formed aluminum foils provide long-lasting protection to ensure the safety and efficacy of medicines and meet the high standards of pharmaceutical packaging needs.
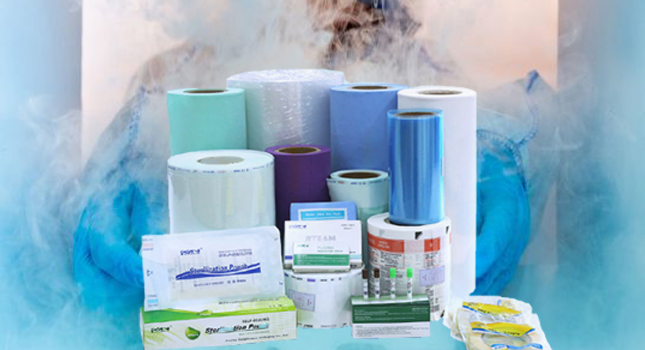
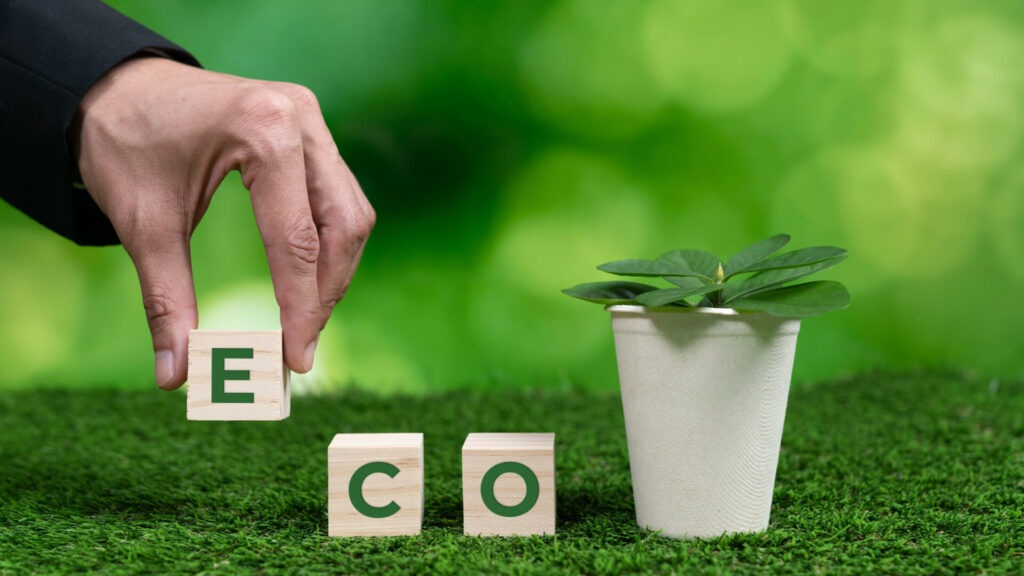
Simplifying The Pharmaceutical Packaging Process
Cold forming aluminum foils can be directly formed, reducing the need for additional processes such as heat sealing or other complex processing steps found in traditional packaging. By optimizing the packaging process, pharmaceutical companies are able to reduce material waste, improve overall operational efficiency and further enhance market competitiveness.
Cold-forming Aluminum Foil Depth Performance
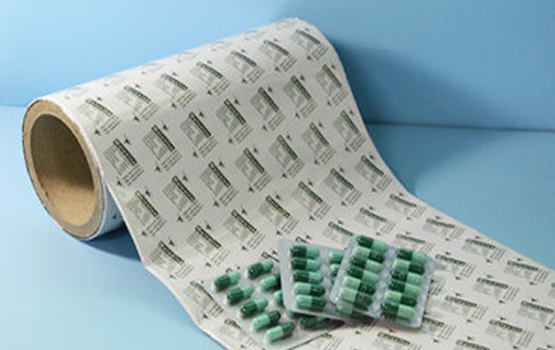
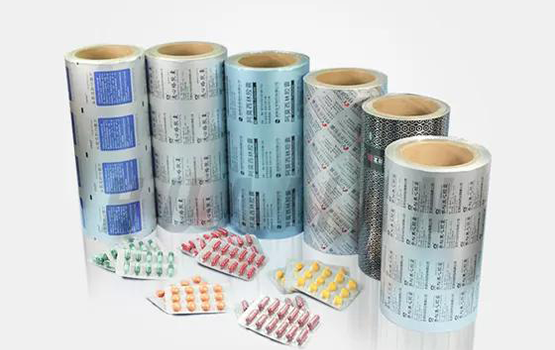
Depth properties of cold formed aluminum foils are particularly important in blister packaging to ensure that their structural strength is maintained during the forming process and to avoid tearing problems caused by packaging that is too shallow or too deep.
1.Depth Forming Capability
Cold forming foils have a high forming capability, allowing the foil to be formed into complex shapes by applying pressure without heat. Compared to conventional thermoformed foils, cold formed foils are able to withstand higher forming depths while maintaining better mechanical strength and are less prone to tearing or breaking. This makes it ideal for use in deeper blister packs, where it can easily wrap around the drug product to ensure that it is not damaged by external pressure or improper handling.
2.High Tear Resistance
Cold forming aluminum foils undergo a precise process during manufacturing to enhance their tear resistance. The depth of the aluminum foil increases the safety of the medicine inside the tablet during blister package forming, reducing the risk of package breakage or medicine leakage. Cold forming aluminum foil has high tear resistance and maintains sufficient strength to ensure the integrity of the package even under higher depth forming conditions.
3.High Precision Molding Capability
The depth properties of cold formed aluminum foil allow for higher precision forming so that each tablet in the package is precisely shaped to fit the drug product. Through precise forming technology, cold formed aluminum foil ensures that the pharmaceutical units are packed at a consistent depth and are less prone to deformation, providing stronger protection against contact with outside air or moisture.
4.Avoiding Ruptures and Cracks
In the process of depth forming, cold formed aluminum foil will not crack or rupture due to excessive mechanical pressure, avoiding the problem of localized cracks that may be encountered with traditional aluminum foil. Deeper blister packs can withstand more pressure and external forces without rupture or loss of sealing, ensuring that pharmaceuticals are well protected during use.
5.Enhanced Closure
The depth of cold formed aluminum foil is designed so that it can be used with PVC, PVDC and other materials to form a strong closure system. Closure is crucial in pharmaceutical packaging. Deeply formed aluminum foil ensures that pharmaceuticals can maintain a hermetic seal under external pressure, avoiding the intrusion of external substances such as moisture and oxygen, and thus improving the stability and shelf life of pharmaceuticals.
The depth of performance of cold-formed aluminum foils makes them ideal for use in pharmaceutical packaging, providing excellent protection and sealing. Whether it's tear resistance, compression resistance, or the ability to form accurately, cold formed aluminum foil meets the stringent requirements of depth forming, ensuring the safety of pharmaceuticals while enhancing the overall performance of the package.
The thickness of aluminum foil affects its strength, stiffness, thermal conductivity and other properties. The greater the thickness, the greater the strength and stiffness, but the thermal conductivity may be reduced.
● Blister packaging for tablets, capsules and softgels
● Ideal for moisture-sensitive drugs that require extended stability
● For packaging of prescription and over-the-counter drugs