Pharmaceutical Aluminium Foil Solutions for Blister Packaging Drug Protection
Pharmaceutical blister packaging is an essential method used to securely package medications like tablets, capsules, and lozenges. This type of packaging provides robust protection against environmental factors such as moisture, light, and oxygen, which can affect the efficacy and stability of the drug. Blister packaging is also designed for convenience, allowing easy tracking of doses, enhancing patient compliance, and offering tamper-evident features. With various types of packaging such as thermoformed and cold-form blisters, this guide explores the different materials, processes, and benefits that make blister packaging an ideal solution for pharmaceutical products.
Key Takeaways:
- Pharmaceutical blister packaging effectively protects medications from moisture, light, and oxygen, ensuring drug stability and efficacy.
- Types of blister packaging include thermoformed blister packaging, cold-form blister packaging, and customized capsule blister packs, each offering distinct advantages for different drug types.
- Cold form blister packaging provides superior oxygen barrier properties, ideal for sensitive biologics, vaccines, and hygroscopic drugs.
- Aluminum foil is a key component in blister packaging, offering excellent barrier performance, regulatory compliance, and recyclability.
- Manufacturing processes for pharmaceutical aluminum foil include rolling, surface treatment, coating, printing, and rigorous quality control to meet regulatory standards.
- Sustainability efforts in the industry are enhanced through recyclable aluminum, lightweight foils, and energy-efficient recycling, supporting the circular economy.
What is Pharmaceutical Blister Packaging?
Pharmaceutical blister packaging involves sealing individual doses of medication—such as tablets, capsules, or lozenges—between a thermoformed plastic cavity (blister) and a lidding material like aluminum blister foil. This method offers:
- Protection: Shields drugs from humidity, light, and contamination.
- Compliance: Simplifies dose tracking for patients.
- Tamper Evidence: Clear visibility of product integrity.
Components of Blister Packaging
- Blister Cavity: Transparent plastic (PVC, PVDC, or cold-form foil) molded to hold the drug.
- Lidding Material: Typically pharma aluminum foil (20–25 μm thick) with heat-seal coating.
- Blister Strip: A connected series of blisters, often perforated for easy dose separation.
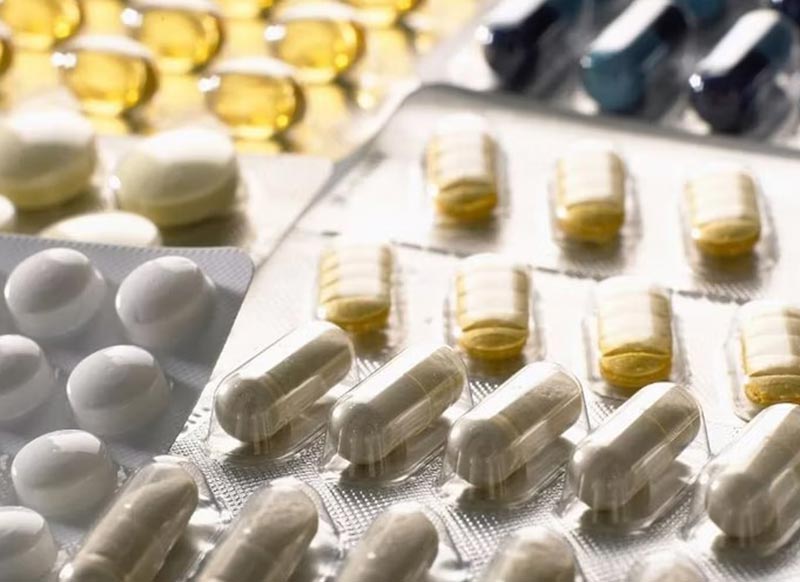
3 Types of Blister Packaging
1. Thermoformed Blister Packaging
Process: Plastic sheets are heated and molded into cavities.
Materials: PVC, PCTFE, or Aclar® for moisture-sensitive drugs.
Use Case: Over 70% of oral solid medications use this method.
2. Cold Form Blister Packaging
Process: Aluminium blister foil is pressed into shape without heat, ideal for oxygen-sensitive drugs (e.g., biologics).
Materials: Multi-layer laminate (Aluminum + nylon + PVC).
Advantage: Provides superior barrier properties—up to 100x lower oxygen permeability than thermoformed blisters.
3. Capsule Blister Pack
Customized blisters to fit capsule shapes, preventing rotation or damage during transport.
The Manufacturing Process: From Raw Material to Pharma-Grade Foil
Step 1: Aluminum Rolling
Raw Material: High-purity aluminum ingots are melted and cast into coils.
Cold Rolling: Reduced to precise thickness (20–25 μm) through sequential rolling mills.
Step 2: Surface Treatment
Cleaning: Removes oils and impurities via alkaline or acidic baths.
Annealing: Heat treatment enhances flexibility and uniformity.
Step 3: Coating & Printing
Heat-Seal Coating: Applied via gravure printing for consistent adhesion.
Custom Printing: Digital or flexographic printing adds branding or safety information.
Step 4: Quality Control
Pinhole Detection: Laser scanners identify defects as small as 10 μm.
Tensile Testing: Ensures foil withstands 15–25 N/15mm sealing forces.
Migration Testing: Validates compliance with FDA leachables standards.
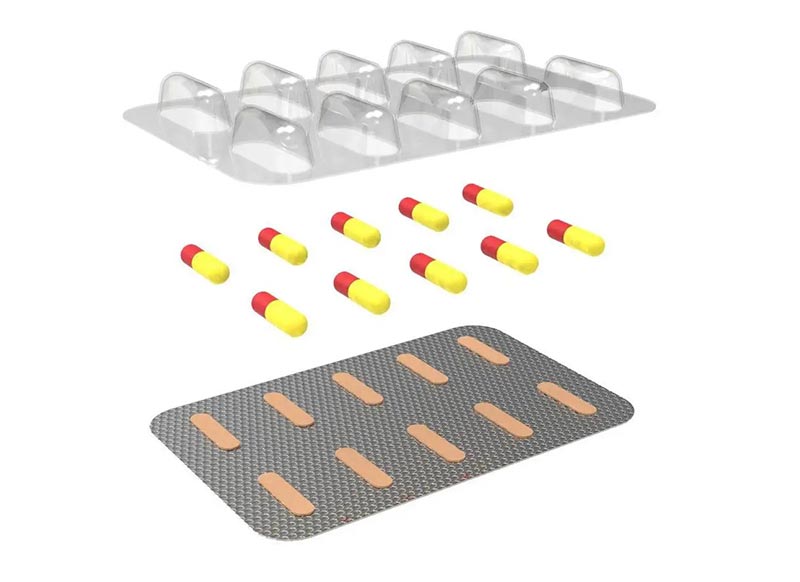
Aluminium Foil Pharmaceutical Packaging
Aluminum foil is a key component in pharmaceutical packaging, offering unmatched protection for medications against environmental factors such as moisture, light, and oxygen. Its unique barrier properties ensure the stability and potency of drugs, making it an essential material in the pharmaceutical industry. Widely used in both blister packaging and laminate forms, aluminum foil helps maintain the integrity of sensitive drugs, such as biologics, vaccines, and antibiotics. Its recyclability and regulatory compliance further enhance its appeal as a sustainable and safe packaging solution.
3 Types of Pharmaceutical Aluminum Foil
1. Standard Pharma Foil
Structure: 20–25 μm aluminum composite film + heat-seal coating (e.g., PVC, acrylic).
Use Case: Ideal for over-the-counter (OTC) tablets and capsules.
2. Cold Form Aluminum Laminate
Structure: Multi-layer laminate (Aluminum + nylon + PVC) for deep-drawn cavities.
Advantage: No heat required during forming—perfect for temperature-sensitive drugs.
Application: Used in cold form blister packaging for biologics, lyophilized products, and hygroscopic drugs.
3. Printed & Coated Foils
Custom Printing: Brand logos, dosage instructions, or anti-counterfeit marks.
Special Coatings:
- Anti-Stick Coatings: Prevent adhesion to blister cavities.
- PCR-Compatible Coatings: Enable recyclability without delamination.
Cold Form Blister Packaging
Cold form blister packaging differs from traditional thermoforming by using hydraulic presses to shape aluminum laminates at room temperature, without the need for heat. This process is particularly beneficial for temperature-sensitive drugs that require the highest level of protection. The ability to form deep-drawn cavities without heat-induced stress ensures that the integrity of the drug is preserved, especially for biologics, vaccines, and other sensitive medications.
The Science Behind Cold Forming
Material Feeding: Multi-layer aluminum laminate (e.g., 45 μm Al + 15 μm PVC) is fed into a press.
Cavity Formation: Dies shape the foil into deep-drawn cavities without heat-induced stress.
Drug Loading: Automated systems fill cavities with precision-dosed medications.
Sealing: A secondary aluminum lidding layer is heat-sealed under controlled pressure.
Result: Airtight blisters with oxygen permeability as low as 0.005 cc/m²/day—ideal for monoclonal antibodies and vaccines.
To see how our Cold Form Aluminum Foil can benefit your packaging needs, explore our product offerings here.
Why Aluminium Blister Foil Dominates Pharma Packaging
- Barrier Performance
Blocks 99.9% of moisture, oxygen, and UV light—critical for drugs like antibiotics and vaccines.
- Compatibility
Works with both thermoforming and cold form blister packaging.
- Sustainability
Recyclable aluminum reduces environmental footprint compared to multi-layer plastics.
- Regulatory Compliance
Meets FDA and EMA standards for leachables, extractables, and child resistance.
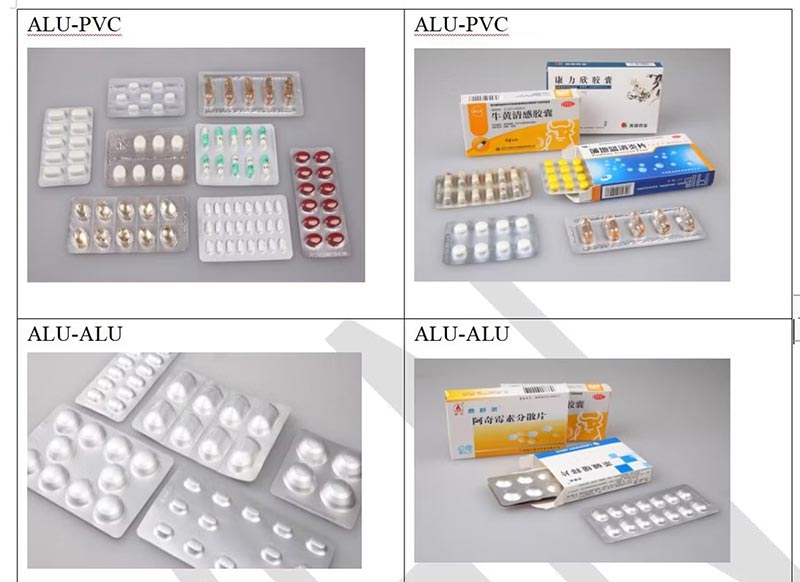
Standard Pharmaceutical Aluminium Foil Packaging
Material Structure
Our pharmaceutical aluminum foil is designed precisely to meet the highest standards required in the pharmaceutical industry. These foils are then supplied to downstream manufacturers for further processing, including printing, molding, and sealing, to create effective pharmaceutical packaging solutions.
Our foil is engineered with precision:
Composite Layer: Through a three-layer process composite synergy, such as OP/AL/VC.
Base Layer: High-purity aluminum (99.5%) rolled to 20–25 μm thickness.
Heat-Seal Coating: Acrylic or PVC-based coatings enable secure bonding to blister cavities.
Printing Layer: Optional eco-friendly inks for branding, dosage instructions, or anti-counterfeit marks.
Customization and Branding
Pharmaceutical aluminum foil can be customized with various branding and functional features, including:
- Custom Printing: Allows for brand logos, dosage instructions, and anti-counterfeit marks.
- Eco-Friendly Inks: Used for environmentally conscious printing, ensuring compliance with sustainability goals.
- Tamper-Evident Features: Printed layers help prevent counterfeiting and tampering, ensuring safety.
These customizable options not only enhance the product’s visibility but also ensure patient safety and compliance with regulations.
Sustainability: Aluminum Foil’s Circular Economy Advantage
1. 100% Recyclability
Aluminum retains its properties indefinitely, making it infinitely recyclable.
Post-consumer recycling rates exceed 90% in Europe, reducing landfill waste.
2. Lightweighting Innovations
Advanced rolling techniques enable 18 μm foils with barrier performance matching 25 μm versions, cutting material use by 28%.
3. Energy Efficiency
Recycling aluminum consumes 95% less energy than primary production, slashing CO₂ emissions.
Choosing the Right Aluminum Foil
Factor | Consideration |
Drug Sensitivity | Use cold form laminates for biologics; and standard foil for tablets. |
Regulatory Compliance | Verify ISO 15378, FDA, and EU GMP certifications. |
Sustainability Goals | Opt for PCR-compatible coatings and lightweight foils. |
Branding Needs | Ensure compatibility with high-resolution digital printing. |
Real-World Applications: How Our Foil Protects Global Health
Case 1: Malaria Tablet Packaging in Tropical Climates
A leading pharma company used our 25 μm cold form laminate to package artemisinin-based tablets in sub-Saharan Africa. Result: Zero moisture damage over 24 months in 90% humidity.
Case 2: Pediatric Antibiotic Adherence
Blister strips with our printed aluminum foil (featuring cartoon characters and perforations) improved dosing compliance by 50% in children under 12.
Case 3: COVID-19 Vaccine Distribution
Our 30 μm aluminum foil ensured the integrity of mRNA vaccine vials during global transit, withstanding temperature fluctuations from -70°C to 25°C.
結論
Pharmaceutical aluminum foil is not merely a material—it is the guardian of global health. From safeguarding life-saving vaccines in extreme climates to ensuring children take their antibiotics correctly, our foil empowers downstream partners to deliver medications with uncompromised safety and efficacy. As the industry advances toward smart packaging and circular economies, aluminum foil remains at the forefront, combining centuries-old reliability with cutting-edge innovation. By partnering with a trusted manufacturer, you secure more than a product; you invest in a legacy of quality, sustainability, and trust.
よくあるご質問
1. What thickness of foil is recommended for vaccines?
A 25–30 μm cold form laminate is ideal for sensitive biologics requiring ultra-low oxygen permeability.
2. Can aluminum foil be used for liquid medications?
Yes! Cold form laminates are compatible with liquid-filled blisters, such as oral polio vaccines.
3. How do you ensure foil compatibility with different drugs?
We conduct extensive migration and compatibility testing under ICH Q1A stability guidelines.
4. What printing technologies do you support?
We offer flexographic, gravure, and digital printing with eco-friendly, FDA-compliant inks.
5. What’s the lead time for custom orders?
Standard orders ship in 4–6 weeks; customized coatings/prints require 8–10 weeks.